1. CONCEPTO. EL SISTEMA
LOGÍSTICO Y LOS FLUJOS MATERIALES Y PRODUCTOS
La Logística se ocupa
de la gestión del flujo físico que comienza en la fuente
de suministro y termina en el punto de consumo.
Esta definición indica
claramente que su campo de acción sobrepasa la mera gestión
del flujo de productos terminados, es decir, es un concepto más
amplio que el tradicional de distribución física. Así,
la localización de plantas y almacenes, los niveles de inventario
y el sistema de información son aspectos fundamentales para la
logística como el almacenaje y el transporte.
La gestión de materiales
se encarga de los flujos de materiales en los aprovisionamientos de
materias primas y componentes y en las operaciones de fabricación,
en el empaquetado de productos terminados. A partir de ese momento,
el flujo de productos terminados, bajo la responsabilidad de distribución,
se dirige hacia el cliente o el usuario final, pudiendo utilizar en
el camino almacenes intermedios.
2. LOS TRANSPORTES EN EL ÁMBITO DEL SISTEMA LOGÍSTICO
DE LA EMPRESA
El costes logísticos
pueden agruparse en cuatro categorías:
- Transporte.
- Almacenaje.
- Inventario.
- Administrativos.
El coste de transporte depende
fundamentalmente del tipo y la actividad de bienes transportados, del
método de transporte y de la distancias a recorrer. Es evidente
que éstas últimas dependen del número de almacenes
y de su localización, y por lo tanto, influirán en los
costes de transporte. A medida que aumente el número de almacenes,
también lo hacen los costes de transporte primario o la larga
distancia, mientras que se reducen los costes de transporte secundario
o de entrega.
3. NECESIDADES DEL TRANSPORTE
La tarea fundamental de la
función del transporte es la de transferir bienes y materiales
entre dos puntos específicos, asegurando que llegan en buen estado,
en el tiempo correcto y a un precio aceptable.
3.1. ELEMENTOS A TENER
EN CUENTA PARA LA ELECCIóN DEL MEDIO DE TRANSPORTE
La elección de un
modo de transporte está directamente relacionada con las necesidades
particulares de la empresa, en términos de:
- Velocidad.
- Fiabilidad.
- Coste.
Además de la velocidad,
la fiabilidad y el coste, hay otros factores que influyen en la elección
del modo de transporte.
Estos son:
Factores operacionales,
que están relacionados con cinco áreas:
- Información respecto
al cliente como: localización geográfica, condiciones
de entrega, características de los pedidos, cargas de retorno,
nivel de servicio requerido, riesgo en los pagos.
- Las características
del producto: tamaño, peso, forma, valor, fragibilidad, deterioro,
peligro.
- Las condiciones de la empresa
tendrán una estructura de producción y almacenaje y una
red de distribución.
- El entorno, tal como las
carreteras, leyes e impuestos, medios de distribución disponibles,
disponibilidad de mano de obra y capital, tecnología, condiciones
climatológicas.
- El modo: ferrocarril, marítimo,
canales y vías fluviales, aviación, oleoductos, carretera.
3.2. FACTORES DETERMINANTES
DE LA ELECCIóN ENTRE TRANSPORTE POR CUENTA AJENA Y PROPIA
La cuestión fundamental
a considerar es si verdaderamente se necesita adquirir vehículos.
Existen dos razones principales por las que muchas empresas encuentran
más económico subcontratar.
La primera es la utilización de los vehículos. La utilización
de los vehículos se puede definir como la proporción de
la capacidad utilizada de los vehículos en relación a
la capacidad disponible. Solamente se alcanza una utilización
del 100% cuando cada vehículo que sale de un almacén va
completamente lleno. Esto es más fácil de conseguir cuando
los puntos de entrega se encuentran cerca del almacén, pero a
medida que las ubicaciones de los clientes se alejan entre sí,
especialmente en áreas distantes geográficamente, se va
haciendo más difícil.
La utilización del
vehículo se refleja en el coste por unidad entregada, necesitándose
un volumen mínimo para que el transportista pueda operar económica
y eficientemente.
La segunda razón son
los costes generales: para que el transporte opere con eficacia, se
necesitan almacenes que proporcionen el soporte necesario. El número
y la ubicación de los almacenes influye considerablemente en
los costes del transporte. Cuanto más amplia sea el área
geográfica cubierta, más almacenes serán necesarios.
De la misma forma, cuanto más cortos sean los plazos de entrega,
más almacenes serán necesarios.
Muchas organizaciones tienen
que satisfacer la demanda estacional o cubrir determinadas áreas
geográficas, a través de la subcontratación o alquiler
de otros vehículos.
3.2.1. VENTAJAS E INCOVENIENTES
DE VEHíCULOS PROPIOS
Ventajas:
- Se pueden construir específicamente
los vehículos para transportar un producto en particular o para
manipular la mercancía.
- Se puede formar al conductor
para que realice adecuadamente su trabajo.
- El conductor puede ser
motivado para que venda la mercancía además de transportarla.
- Los vehículos pueden
llevar logotipo de la empresa.
- La empresa retiene el control
absoluto sobre el vehículo y su operación.
Inconvenientes:
- La gestión del transporte
puede ocupar mucho tiempo a la dirección, requiere unos conocimientos
específicos e implica una inversión de capital significativa.
- Los transportistas pueden
ofrecer unos servicios más baratos que los que se puede obtener
con transporte propio.
- Cuando el mercado es muy
estacional, las empresas que utilizan su propio transporte necesitan
una compleja mezcla de vehículos propios y alquilados para llevar
a cabo una operación eficiente.
3.2.2. VENTAJAS E INCONVENIENTES
DE LA SUBCONTRATACIóN
Ventajas:
- Se dispone de la flexibilidad
necesaria para responder a la demanada estacional.
- Se pueden resolver con relativa
facilidad los problemas de cargas y rutas variables.
- El transportista puede ofrecer
un servicio más eficiente.
- La administración
de los vehículos y conductores pasa a ser responsabilidad del
subcontratista. Esto permite a la propia empresa concentrarse en otras
áreas más productivas.
- Se elimina o reduce la necesidad
de inversión de capital en el transporte.
- Se reducen los problemas
laborales.
Inconvenientes:
- Se pierde parte del control
y puede afectar al servicio al cliente.
- Fluede generar problemas
de incapacidad de atender demandas especiales.
- Se reduce la capacidad de
controlar el producto.
- A veces no se puede llevar
el logotipo en los camiones y se pierde oportunidades de realizar publicidad.
- Cuando el mercado no es
estacional, la operación con vehículos propios es frecuentemente
más económica.
3.3. ELEMENTOS A TENER EN CUENTA EN LA PROGRAMACIóN DE TRANSPORTES
La programación de
vehículos, orientada a conseguir rutas óptimas y máxima
carga de los vehículos, es particularmente importante en la distribución
minorista, donde se realizan entregas tanto a clientes locales como
a clientes distantes en otras partes del territorio. El procedimiento
de programación de vehículos implica, básicamente,
la entrega de cantidades determinadas de artículos con vehículos
de capacidad conocida. Se supone que los artículos se entregan
desde un almacén fijo y que se conoce la localización
de cada uno de los clientes.
Puede haber restricciones
en el funcionamiento de los vehículos debidas al horario de trabajo,
a la longitud total de los viajes diarios y al número de entregas
que se pueden hacer en la jornada normal de trabajo. Una solución
aceptable del problema de programación de vehículos debería
proporcionar las rutas óptimas que satisfacen las demandas de
los clientes y que tienen en cuenta las restricciones legales y los
recursos disponibles por parte de la empresa.
El análisis implica
una investigación de todas las posibles rutas, suponiendo las
siguientes condiciones de funcionamiento:
- Está limitado el
número total entre las que se puede hacer a un cliente particular
en un día.
- Está limitada la
distancia total recorrida por un vehículo en un día.
- Los vehículos tienen
una capacidad de cara fija.
- Se conoce la demanda de
productos de cada cliente.
- La cantidad de productos
servida a cualquier cliente es menor que la capacidad de carga de los
vehículos.
Una solución satisfactoria
proporciona una programación de rutas que minimiza la distancia
total recorrida o el tiempo que los vehículos están en ruta.
Las técnicas de programación de vehículos se pueden
utilizar también para establecer el número óptimo
de vehículos, de una determinada capacidad, necesarios para una
nueva flota o para una flota mejorada.
La carga de un vehículo
se determina suponiendo que:
- La capacidad de los vehículos
es limitada.
- El tiempo de conducción
de cada conductor está limitado.
- Cada pedido tiene un destino
para el que se conoce la duración del trayecto desde el almacén
hasta el destino y viceversa, o la duración del trayecto hasta
el próximo cliente.
- Cada pedido contiene una
cantidad específica de productos para la que se conoce el tiempo
necesario para realizar su descarga o su carga en las instalaciones
del cliente.
Para calcular la carga
de un vehículo se realizan consecutivamente las siguientes operaciones:
- Se determina el tiempo
de viaje desde el almacén hasta el cliente.
- Se le añade el tiempo
de descarga en las instalaciones del cliente.
- Se comprueba que no se
excede el tiempo disponible del conductor.
- Se comprueba que no se
supera la capacidad de carga del vehículo.
A continuación, se
añade el siguiente pedido, que será el que se encuentre
geográficamente más próximo, y:
- Se determina el tiempo
de viaje desde el primer cliente hasta el siguiente.
- Se le añade el tiempo
de descarga en las instalaciones del cliente.
- Se comprueba que no se
excede el tiempo disponible del conductor.
- Se comprueba que no se
supera la capacidad de carga del vehículo.
El proceso se repite hasta
que se esté cerca de alcanzar una de las restricciones, y será
entonces el momento de intentar añadir un pedido final que complete
el tiempo disponible del conductor o complete la carga del vehículo.
Este procedimiento se repite hasta que se hayan asignado todos los pedidos
o estén completamente cargados todos los vehículos.
4. DETERMINACIÓN DE LA RUTA DE LOS VEHÍCULOS
Los tipos de rutas que se
emplean habitualmente son tres:
Rutas
de arco o circulares, que unen a los clientes con distancias similares
al almacén formando arcos.
Rutas de zona, que
unen a los clientes concentrados en una zona
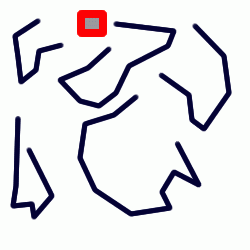
Rutas radiales, que
unen a clientes a lo largo de caminos radiales desde el almacén.
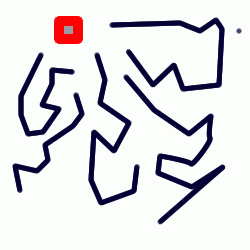
El tipo de ruta depende de varios factores:
- Las técnicas utilizadas
para hacer la programación de entregas.
- Las características
geográficas de las zonas.
- La relación entre
el tamaño de los productos que componen los pedidos y la capacidad
de los vehículos.
Cada tipo de ruta tiene características
diferentes. Cabe destacar que las rutas de arco obligan a recorrrer
una distancia mayor, ya que la distancias del primer y del último
cliente de la ruta al almacén son significativarnente mayores
que en los otros tipos de rutas.
4.1. MÉTODOS DE
PLANIFICACIóN DE RUTAS
4.1.1. MÉTODO DE
LOS AHORROS
El método más
conocido de planificación de rutas es el llamado "método
de los ahorros". Constituye la base de muchos sistemas de planificación,
tanto manuales como informatizados.
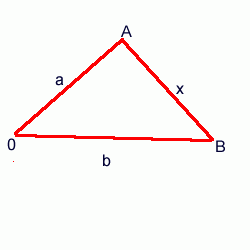
Supongamos que es necesario
servir a los clientes A y B desde el almacén 0.
Una primera ruta que se puede
utilizar consiste en ir de 0 a A y volver al almacén, para, posteriormente,
ir de 0 a B y volver. En este caso, la distancia recorrida será:
a+a+b+b=2a+ 2b.
Una ruta alternativa a la
anterior es O-A-B-O. En este caso, la distancia recorrida es:
A + b + x
El ahorro conseguido por la segunda ruta es:
(21+2b)-(a+b+ x)=a+b-x
Se puede destacar varios
aspectos:
- El ahorro nunca es negativo.
El menor valor que puede tomar es cero, ya que un lado de un triángulo
siempre es menor o igual a la suma de los otros dos lados.
- Encadenar varios clientes
aumenta el ahorro.
- Cuanto más cerca
estén los clientes entre sí y más alejados del
almacén, más ahorros se conseguirán.
- Las rutas de arco proporcionan
los mayores ahorros.
- Se puede utilizar el tiempo
en lugar de la distancia.
Es necesario programar las
entregas a cuatro clientes A, B, C y D desde el almacén 0. La
distancia recorrida en una ruta no puede exceder de 75Km.
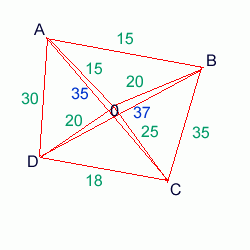
Paso 1. Cálculo
de los ahorros para todas las parejas de clientes:
|
A
|
B
|
C
|
D
|
A
|
0
|
20
|
5
|
5
|
B
|
|
|
10
|
3
|
C
|
|
|
|
27
|
Paso 2. Comenzando
por el ahorro mayor, se van uniendo clientes hasta que se alcance una
restricción.
Empezando con el ahorro máximo,
que es 27, se unen los clientes C y D.
La distancia O-C-D-0 es de 63, inferior a la restricción.
El siguiente mayor ahorro
es 20, correspondiente a la pareja A-B. Se unen A, B, C y D.
La distancia O-A-B-C-D es
mayor de 75, por lo que la ruta no es admisible.
Se toma el siguiente mayor
ahorro, que es de 10 y, por lo tanto, se unen B,C y D.
La distancia O-B-C-D-0 es
mayor de 75, por lo que la ruta no es admisible.
El siguiente mayor ahorro
es 5, por lo que se unen A,C y D.
La distancia O-A-C-D-0 es
mayor de 75 y la ruta tampoco es admisible.
Paso 3. Se ha terminado
de analizar la lista. La primera ruta será, por tanto, O-C-13,
ya que las demás no cumplen con la restricción de distancia.
Paso 4. Se vuelve
a escribir el cuadro anterior, eliminando las filas y las columnas correspondientes
a los clientes C y D, ya asignados a la ruta.
Paso 5. Se comienza
de nuevo el proceso, empleando por el mayor ahorro, que es de 20 y une
los puntos A y B.
La distancia O-A-B-O es de
50 y constituye la segunda ruta.
4.1.2. SISTEMA SDS
Es un sistema de planificación
de cargas divide el área geográfica que cubre un almacén
en subáreas. A cada una de ellas se le asigna un código
compuesto por dos caracteres: uno alfabético y otro numérico.
El código alfabético hace referencia a las principales
rutas, normalmente radiales, que salen del almacén y pasan por
la subárea, mientras que el código numérico indica
el tamaño de la subárea, el cual viene determinado por
las características geográficas, por una concentración
de clientes potenciales.
Para la determinación de la rutas, el planificador comienza por
la subárea más alejada del almacén y va componiendo
la ruta, siguiendo por las subáreas del mismo código alfabético
en dirección al almacén.
El sistema original no tiene
en cuenta los tiempos de desplazamiento desde o hacia las subáreas
o dentro de las propias subáreas. Sin embargo, en ocasiones se
contemplan estos tiempos. La principal ventaja de este método
es que se pueden reflejar correctamente las características geográficas
del área a cubrir, lo que produce rutas excelentes, que son aceptables
tanto por la dirección como por los conductores.
4.1.3. SISTEMA TRANSIT
Este sistema también
se basa en un mapa, el área de entrega se divide en cuadrados
de 10 Km de lado. La localización de cada cliente viene dada
por el cuadrado en el que se encuentra. A cada cuadrado se le asigna
un tiempo de conducción desde el almacén y un tiempo de
conducción dentro del propio cuadrado.
Se ordenan los pedidos en
un casillero según el cuadrado al que se pertenezcan.
Se identifica el cuadrado
más lejano del almacén.
El cuadrado seleccionado
se subdivide en áreas de 1 km.
Se empieza a componer la
carga empezando por la casilla de 1 km de lado más alejada del
almacén.
Cuando se asignan los pedidos
, se calcula el tiempo total, una vez asignados los pedidos de un área
de 10 Km cuadrados, se continúa con la siguiente en la dirección
del almacén.
4.1.4. MÉTODO DEL
RELEVO
Se produce cuando dos vehículos
articulados viajan regularmente desde lugares diferentes a un almacen
intermedio. La operación se puede organizar de tal modo que los
camiones via en al almacén intermedio por la j
mañana y recojan un remolque para realizar el reparto a nivel
local por la tarde. Cada camión puede coger el remolque del otro
para llevarlo en el viaje de vuelta. De esta manera, cada camión
puede realizar tanto el transporte de larga distancia, como el reparto
a nivel local desde el almacén intermedio.
4.1.5. MÉTODO DEL INTERCAMBIO
Cunado para cubrir el trayecto
de ¡da y vuelta entre dos almacenes distantes entre sí,
es necesario realizar una parada durante toda la noche para el descanso
de los conductores y continuar el viaje a la mañana siguiente,
se pueden utilizar dos vehículos articulados y disponer de un
punto de transferencia a una distancia equidistante de los dos almacenes.
De este modo, los camiones
pueden intercambiar su carga en el punto de transferencia y volver a
su punto de origen. El viaje de ¡da y vuelta se puede realizar
en el mismo día.
|